Faced with a sudden yield drop of over 4% and increased variability at a single-drug manufacturing facility, Recordati set out to uncover the root causes behind the fluctuations. Despite maintaining full compliance with regulatory standards, the pharmaceutical group faced two major obstacles: fragmented data scattered across silos and limited resources for conducting in-depth analytics.
Determined to address these challenges, Recordati partnered with Aizon to leverage AI-driven insights and advanced data integration capabilities.
Understanding the Problem
The facility's yield challenges were compounded by traditional systems that relied on paper-based batch records, third-party systems housing production data, and quality certificates stored as PDFs. The lack of consolidated data made it nearly impossible to gain actionable insights. Additionally, the limited analytics resources meant that identifying and implementing solutions required innovative approaches.
Deploying a Solution
The collaboration began by integrating and contextualizing diverse data sources into Aizon's platform. This included process data, material attributes, batch records, and even previously inaccessible sensor data. Using a CRISP-DM methodology—an iterative, cross-industry standard for data mining—Aizon's data science team worked closely with Recordati’s subject matter experts to ensure every insight was actionable and aligned with operational goals.
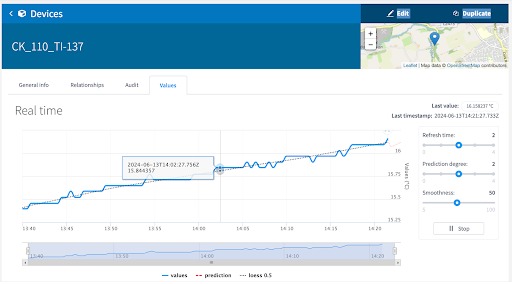
Through two levels of root cause analysis, the team identified key process parameters (CPPs) that were directly impacting yield. Predictive regression models revealed relationships between variables such as drying time and product consistency, while correlations between external factors like seasonal temperatures and yield variability pointed to opportunities for process optimization.
Time series analysis played a critical role in understanding batch-to-batch variations. Using AI models, the team clustered sensor data to identify patterns and behaviors impacting yield. Additionally, they analyzed metrics like median, maximum, and slope from time series data, gaining insights into both individual and combined variable effects on yield. For example, initial analysis of six sensors has already uncovered differences in operator performance, prompting efforts to refine batch records for more consistent outcomes.
Further analysis identified raw material quality as another key factor affecting yield. While the current quality is within acceptable ranges, it is actively monitored to ensure consistency. Any decline in raw material quality could significantly impact yield, making it a critical variable for continuous monitoring and control.
These insights set the stage for Recordati to move beyond diagnostics and implement actionable changes to streamline their operations.
From Insights to Industrialization
To translate insights into action, Recordati implemented targeted process changes, which included refining drying times to achieve optimal levels of dryness and deploying dashboards for real-time process monitoring. The dashboards provided a comprehensive view—from batch-level analysis to trend monitoring—empowering operators to proactively address deviations before they escalated.
A recent process change involved increasing the duration of one heating process after detecting a correlation between its duration and yield.
Building on these insights, the team is implementing two additional process changes. First, batch records are being enhanced to provide operators with clearer, more detailed instructions, reducing variability and improving outcomes. Second, the engineering team is investigating how to stabilize washing temperatures, as seasonal water temperature fluctuations have been linked to variability in yield. These changes aim to further optimize process consistency and performance.
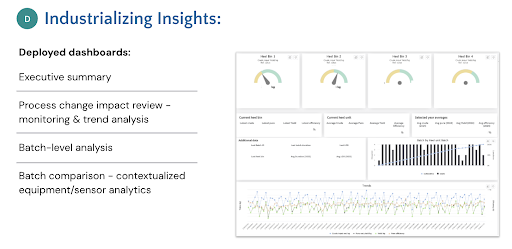
Moreover, Aizon enabled the digitization of previously manual workflows, such as extracting data from certificates of analysis (CoAs) using OCR technology. This automation not only reduced manual effort but also ensured that insights could be generated and applied in near real-time. Additionally, it significantly reduces human errors, given that when copying data manually it’s easy to make mistakes such as changing the format, replacing a comma with a period, or entering an incorrect number.
To support these advancements, all data sources are being consolidated into a unified system. This integration simplifies data management, reduces inconsistencies, and provides a centralized platform for advanced analytics. For Recordati, this means faster decision-making, greater operational efficiency, and a stronger foundation for continuous improvement.
“The collaboration with Aizon empowered our team to uncover the root causes of yield variability and implement changes that delivered immediate results. By leveraging AI and real-time insights, we’ve taken a significant step towards a more stable, efficient, and intelligent manufacturing process."
Davide Botta, Recordati
Achieving Results
Within three months of implementing the solution, Recordati achieved a 1.5% increase in yield, reducing cost of goods sold (COGS) by 2%. Beyond the financial gains, the initiative also reinvigorated the plant’s workforce. Operators became more engaged with the modern tools at their disposal, fostering a renewed commitment to continuous process improvement and operational excellence.
A Path to Intelligent Manufacturing
Recordati’s success demonstrates the power of combining AI-driven insights with human expertise. The partnership with Aizon not only resolved immediate yield challenges but also laid the groundwork for a future of intelligent GxP manufacturing. The roadmap ahead includes further automation of data entry, real-time monitoring through an AI-powered SaaS application, and proactive interventions to maintain peak efficiency.