What does the future look like in a smart factory in the pharma or biotech industry? We believe a smart factory is a digitally transformed facility and operation that is reaping the benefits of increased productivity. In fact, some experts predict an order of magnitude productivity gain! It is this productivity gain we need to aim for and think about when talking digital transformation, it is the vision and the clear long-term goal. And yes, it is super important because with a clear goal it is easier to prioritize which technology to try first and where or what to digitally transform first, in other words, the strategy.
That being said, it is not easy to paint a precise picture of what that factory should look like because we really can’t predict the future – we still don’t have the DeLorean time machine just yet. There are a number of technologies that have still not matured and many more interesting technological advances that we have not seen thus far. We can, however, draw a picture of how such a factory behaves and where we can clearly see productivity increases. We have in fact done this in the past, research in the 90s already drew a picture of smart factories and some of the related technologies such as IIoT. And of course, we can also learn from experiences from industries outside of the life sciences that are using some of the available technologies, are further along in their digital transformation, and enjoying higher levels of productivity.
One area where technology adoption is lagging is IIoT enablement of pharmaceutical and biotech manufacturing equipment. What we envision in the future is collaborative and connected manufacturing processing, equipment and devices. For example, imagine a future where bioreactors are smart, with built-in capabilities to analyze the process in real time using AI with predictive analytics.They continuously collect and stream data to the cloud in order to receive predictive insights about their process based on external parameters. They also can select and use predictive models made available from an ‘app store’ in the cloud. Each model has been rated by others (other bioreactors, process experts, etc.) on how good they are for certain situations such as product, material, type of equipment, environment, etc. At the same time, these bioreactors are collaborative. For example, they can interact with other manufacturing equipment to automatically coordinate material control, get material attributes, instruct on optimal cleaning, how to charge, and much more. They can also interact with other bioreactors to learn and improve processes, the performance of predictive models, or get current process metrics. The smart bio-reactors are collaborating with the operators, like using AR or thru wearable HMIs to instruct them on what the next process steps are, adjusting media feeds, alerts, and quality performance.
Automation has been around for decades, so why is this advanced collaboration and self-driving performance important and where is the real value? Well, it has to do with the adaptive behavior that these smart systems can exhibit. Since the process behavior is dynamic and ever changing, the only way to get consistent performance is by having adaptive control. Not only can adaptive control manage the ever-changing nature of the process’ both internal and external factors, but it can also continuously learn, improve and thereby consistently increase performance and quality.
This all seems very much like a “back to the future” scenario, because at the end of the day, that is what it is. In today’s environments the level of sophistication of pharma equipment is still very much in the Industry 3.0 “automation” and in many cases even “island of automation” levels. Although there is some interesting technology that is available now to start piloting like AR and VR and some advanced IIoT sensors, real adoption remains limited until the technology and equipment suppliers have developed further. So what technologies are ready now? Cloud computing and IIoT are past the ‘peak of inflated expectations’! From that perspective, we should waste no time – the future is truly here!
Using IIoT, the ease of which data can be sent to the Cloud often requires a second look. We have been fighting the connectivity and data contextualization problem for such a long time that it’s hard to believe it can be done any other way. If we take a deep breath, step out of the ditch, and take a look around, we will quickly realize that we don’t need to do this anymore! Data can be collected by software agents running on everything from a server to a sensor and configured through a digital twin. There is no need to format, convert, transform or contextualize the collected data. In fact, the AI and ML algorithms work best if we keep it unstructured, and the smaller the data sets the better.
Technologies such as big data, advanced analytics, including AI, used on a cloud computing platform are ready for digital prime time. As individuals, we use it every day (even if it’s not immediately apparent to us). In the smart factory, cloud services will provide a holistic overview of the manufacturing operations, processes, and supervisory control. Manufacturing intelligence using big data will provide visibility, insights, and perspective on what is going on in the manufacturing operations. Advanced analytics and AI will provide predictive insights that can at a minimum be used for improvement and ultimately lead to radically increasing performance – process, operation, and quality! Of course, this requires that all data about the factory be accessible and interpretable by all the different aspects involved in running the factory, from humans to building, to equipment and down to sensors.
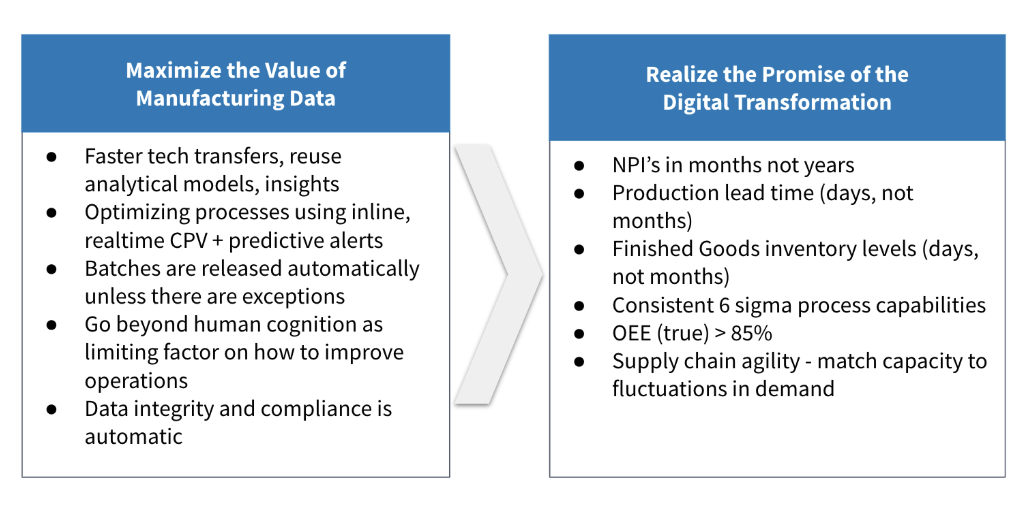
So if you had all possible information at your fingertips – what problems would you be solving? The ability to have a real-time picture of everything that is going on in our manufacturing plant is simple and achievable. On top of that, we can discover relationships between processes and artifacts that we never imagined existed. We can use this information to improve, better operate, and maybe stop the great firefight that is operating a plant. That in itself will directly result in a productivity increase. In a smart factory of the not so distant future, we will see highly productive and flexible operations, where the same equipment is used for a range of different products and modalities, where tech transfers for new commercial products happen within weeks, where only very few batches require extensive QA reviews prior to release, where...
What is your perspective on “smart manufacturing”, your picture of back to the future?